Overview
United States Cold Storage (US Cold), an industry leader in providing cold storage solutions and logistics services, faced complex customer demands and rising operational challenges at its McDonough, GA site. To keep pace with varied client requirements and industry pressures, US Cold sought an automation solution that could deliver efficient, high-density storage and accommodate multiple product types. Westfalia’s automated storage and retrieval system (AS/RS) was the ideal answer, bringing increased throughput, optimized space, and adaptability to US Cold’s 3PL operations.
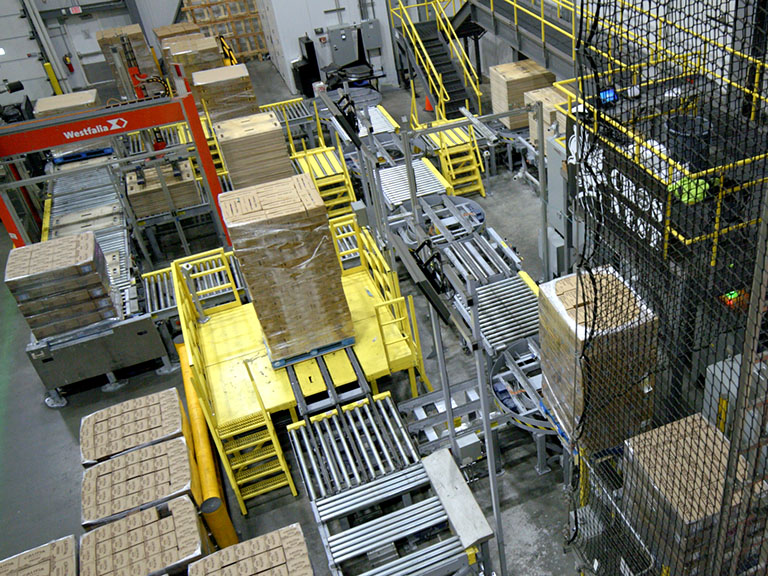
Challenge
US Cold’s McDonough facility faced several significant operational challenges that called for a flexible, high-performance solution. As a 3PL provider, US Cold managed a broad range of customers and their SKUs and storage conditions demanding a system that could quickly adapt to shifting customer needs. The requirement for both reliability and flexibility added complexity, as the solution needed to maintain high service levels across various inventory demands. Additionally, labor shortages and high turnover in the McDonough area strained resources, making it challenging to keep up with growing demand using conventional storage methods. US Cold recognized that automation was essential to achieving the throughput needed to meet client expectations while reducing reliance on manual labor.
Space constraints further compounded these challenges. Limited land availability led US Cold to consolidate two proposed facilities into a single high-density site, requiring a solution that could maximize storage capacity within the available footprint. The AS/RS would need to accommodate both freezer and cooler functionalities within this compact space while still delivering the efficiency, speed, and flexibility critical to the operations. After evaluating several vendors, US Cold found that Westfalia stood out, not only for the technical solution offered but also the partnership-oriented approach, treating US Cold as a valued partner rather than just a customer.
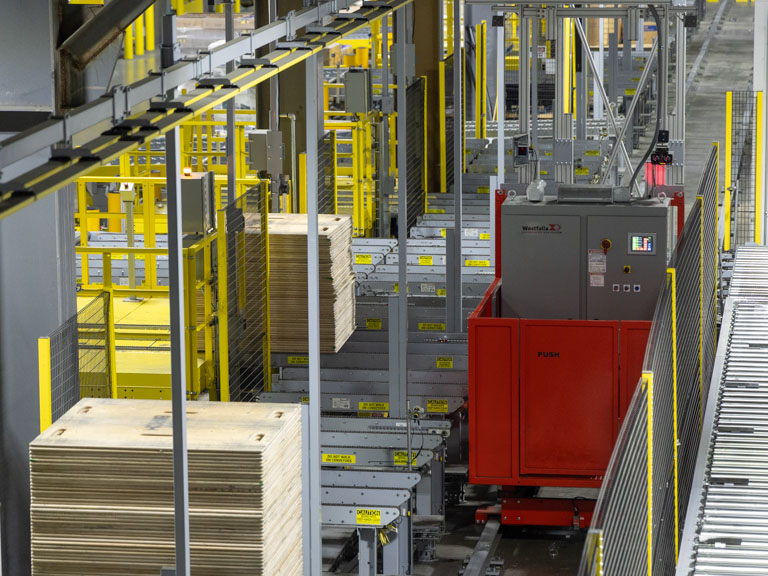
The McDonough site was divided into two “rooms”: a freezer dedicated to a key client and a flexible cooler area for diverse inventory. This adaptable setup allowed US Cold to adjust storage configurations based on evolving client needs.
Tandem cranes in the Room 5 cooler move two pallets simultaneously, enabling faster throughput. A dual-level conveyor system separates inbound and outbound operations, allowing for smoother pallet flow. The design feeds all outbound pallets through gravity flow, making them ready for quick truck loading. Additional staging was added on the dock to balance the flow between the AS/RS and truck loading operations.
Layer and case picking were incorporated directly into the racking of both the cooler room and freezer, maximizing space and minimizing unnecessary footprint. This design supports efficient order fulfillment while maintaining high storage density. Pick tunnels were provided in the racking of both the cooler and freezer areas. The picking configurations in this AS/RS include layer picking, pick-to-pallet jack, and pick-to-belt, ensuring US Cold has comprehensive picking options to meet any client request. Replenishment to picking is fully automated in both temperature-controlled zones.
Westfalia’s triple-rail design, combined with pallet support boards (PSBs), ensures that all pallet types are safely supported. This added stability prevents deflection and minimizes product damage, especially important in a high-stress cold storage environment.
The Savanna.NET® Warehouse Execution System (WES) seamlessly integrates with US Cold’s existing software, enabling real-time inventory adjustments, automated replenishment, and streamlined management of diverse SKUs. Westfalia’s dedicated support team worked closely with US Cold to tailor the software, providing continuous collaboration to ensure that the system met their specific needs.
Solution
Westfalia worked closely with US Cold to design and implement a custom AS/RS that met these challenges effectively.
System Features
143,000 sq. ft.
47,155 pallet positions
Nine (9) storage/retrieval machines (SRMs)
Pallet-Support Board (PSB) handling
Westfalia Automated Layer Picker
Savanna.NET® Warehouse Execution System (WES)